One-stop shopping Felt lampshade molding solutions
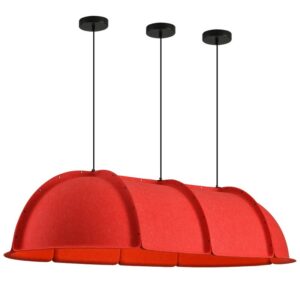
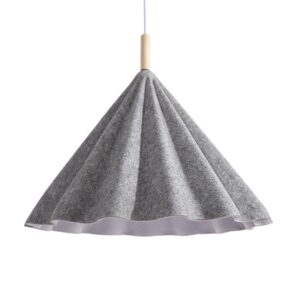
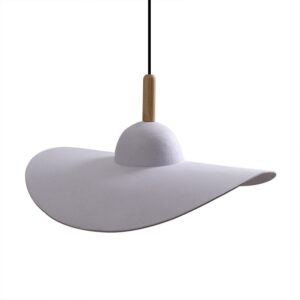
Apartment Felt lampshade
- 13725883619
- huajiajixie@126.com
- www.huajiayeya.com
Successful Transformation of Felt Lampshade Manufacturer
One of our clients, a company specializing in the production of felt lampshades, had been struggling for a long time to find the right equipment to meet their production needs. Despite multiple attempts, they were unable to find the appropriate solution, resulting in an inability to produce their products efficiently. Then one day, they came across our video on YouTube and realized that our equipment was the perfect fit for their requirements. After detailed communication, we gained a deep understanding of the client's production process and specific needs. We quickly customized a comprehensive equipment configuration plan for their felt lampshade production. Not only did we provide the molding equipment, but we also assisted in mold development, sample production, and machine debugging to ensure the production process ran smoothly. Ultimately, the client was highly satisfied with the equipment and services we provided, successfully resolving their production challenges. With our support, the client purchased several sets of lampshade molds and 3 sets of felt forming machines, significantly improving production efficiency and solving the equipment problems they had been facing for years. They are now able to consistently produce high-quality felt lampshades. Through this case, we demonstrate that our company not only offers advanced equipment but also provides comprehensive technical support and solutions tailored to meet client needs, helping them achieve efficient production and business growth.
One-stop shopping EVA shoe material molding solution



Apartment EVA shoe material
- 13725883619
- huajiajixie@126.com
- www.huahuiyeya.com
EVA Footwear Molding Equipment Solution
This customer specializes in EVA footwear production and initially faced significant challenges in finding the right molding equipment. Due to the high requirements for molding quality, precision, and production volume, they had tried several types of equipment without success. The first attempt involved high-frequency equipment and a copper mold, but the results were unsatisfactory. The second attempt was with a heat press machine, but again, they couldn’t achieve the desired results. After several setbacks, the customer found our equipment demonstration through a short video platform and reached out to us.
After in-depth communication, we identified the root cause: the customer was using the wrong process. The correct process for EVA footwear molding is to first bake and then press, which the customer hadn’t considered. We provided professional guidance on the correct process and helped them set up an aluminum mold for testing at our facility. With precise adjustments, the EVA footwear molding was successfully completed, and production efficiency was significantly improved.
Once the testing was successful, the customer was very satisfied with the equipment’s performance and molding results, and immediately ordered 4 sets of equipment for mass production. They commented, “We’re so glad we saw your video. Otherwise, we wouldn’t know how many more detours we’d have to take
Thanks to your professional support, we’ve finally found the right equipment and process. Our production efficiency and product quality have greatly improved. We really appreciate your help — without it, we’d still be struggling to find the right solution


Apartment Electronic Industry Assembly Parts
- +(86)13609698250
- huajiajixie@126.com
- www.huahuiyeya.com
Electronic Pressed Products Solutions
Customer Background: The customer is a manufacturer in the electronic industry, specializing in the production of high-precision electronic components.
Customer Issues: The customer faced several challenges with their existing stretching machines, including inaccurate pressure settings, air pressure fluctuations, and aging equipment. These issues were affecting the precision of their production, leading to lower product quality and reduced efficiency.
Solution: We provided the customer with high-precision four-column stretching machines, equipped with advanced pressure and position sensors. These sensors ensure that every assembly operation is performed with precise pressure and positioning, eliminating interference from external factors and ensuring consistent results.
Outcome: After six months of using our equipment, the customer was highly satisfied with the stability and precision of the machines. As a result, they immediately placed an order for 10 additional four-column stretching machines to further improve production capacity and efficiency.
Customer Feedback: The customer expressed great satisfaction with both our pre-sales and after-sales services, particularly our professional technical support and equipment debugging services, which ensured the long-term stable operation of the machines.